
A Spin on Efficiency: Generating Tomorrow's Electricity from Better Turbines
May 12, 2010 - David Biello - scientificamerican.com
Improving turbines, which lie at the core of a modern power grid, is all about standing up to the heat
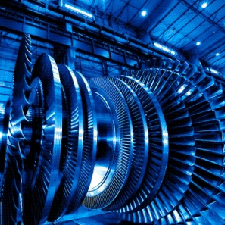 |
SPIN-TRONICS: Generating electricity generally involves spinning a turbine with steam, or burning gas or using wind. |
Courtesy of Alstom |
At the spinning heart of the modern electric grid lies what used to be called the dynamo—a generator composed of stacks of copper rotating in an electromagnetic field. But it's a turbine that spins the dynamo—and efforts to squeeze more efficiency and cut greenhouse gas emissions and other pollution from a smart grid may rest on improving this core technology.
"The best emissions are emissions you don't make in the first place," notes Charles Soothill, senior vice president for technology at Alstom Power, a maker of turbines.
Heating water into steam to spin a turbine is the basic principle behind most power generation. Today, for instance, the firebox of the Mountaineer power plant in New Haven, W.Va., consumes nearly 14,000 kilograms of coal a minute, enabling the plant to pump out 1,300 megawatts of power. Reaching temperatures of more than 500 degrees Celsius, the steam pours through pipes and around a turbine—a 200-metric-ton, 30-meter-long steel shaft outfitted with blades and vanes to help it spin as the steam expands and cools.
That mechanical spinning in turn rotates copper-filled tubes in a magnetic field. This induces current in the copper, which then courses through the modern electricity grid—a giant circuit—to your house.
"Steam turbines and gas turbines are a means of converting power in the form of either steam or gas into mechanical power and electricity," Soothill explains. "These machines have been around for a long time—more than 120 years."
In that time, the basic principles of a spinning turbine have not changed much. The majority of power plants—whether coal, natural gas, nuclear or even wind—rely on a turbine to spin the generator and produce vast quantities of electricity. Improving these turbines saves fuel and pollution. "You can save 9 billion pounds of CO2 per year from a one-point efficiency improvement," says engineer Eric Gebhardt, a general manager at General Electric (GE) Energy, another turbine maker.
Spin cycle
Fashioning a new steam turbine from a specially shaped hunk of steel takes roughly 18 months, and that includes making titanium blades as long as a person's arm. Ultimately, the turbine will spin at speeds up to 3,600 rotations per minute (1,800 rpm for the larger steam turbines required at a nuclear power plant). The turbines, designed to last at least 20 years, must withstand the nontrivial impacts from water droplets traveling at high speed as well as temperatures as high as 620 degrees C, among other challenges. "The hotter the equipment operates, the more efficient it becomes," Soothill notes.
Of course, metals such as steel tend to soften when exposed to high temperatures—and that can cause parts to wear out prematurely. Nickel alloys mixed with the steel improve the turbine's heat resistance and may enable operation at 700 degrees C by 2020, Soothill says. Such a temperature would enable coal plants to capture 50 percent of the energy released by coal burning, up from an average of roughly 40 percent today.
GE is exploring carbon fiber and ceramics from silicon carbide composites to permit higher temperature operation. Greg Corman of GE's Advanced Ceramics Lab notes that the company is now evaluating the ceramics on a test turbine in its Lynn, Mass., facility, although these new materials may see application in jet engine turbines before power plants. "It's 50-50 either way," he says.
The future is a (natural) gas
Even though a nuclear power revival may be under way—along with new turbines being retrofitted into existing plants that have had their license to operate extended by several decades—demand for steam turbines is not strong in the U.S., in large part because utility companies now want electricity-generating sources that can be stopped and started more flexibly and cleanly. "It's hard to start up a coal plant with a phone call," Gebhardt says. "In a carbon-constrained world, gas will play a larger and larger role."
In fact, "gas is filling the gap" given the slow start of the nuclear renaissance and the black reputation of coal, says Richard Pangrazzi, director of regional marketing for Alstom in North America. Natural gas not only offers a 40 percent saving in terms of CO2 emissions compared with coal burning, but also can reliably back up more variable—and increasingly popular—electricity-generation sources, such as wind turbines or solar panels, thanks to its ability to start up in minutes.
Gas turbines come in several varieties, ranging from basically a jet engine strapped to the ground to a combined-cycle unit that burns the gas in pressurized air to spin one turbine and then captures the heat from that process to make steam to spin a second turbine. But they work just like steam turbines: using hot, high-pressure gases—in this case the product of combusting natural gas—to create spin. "Combined-cycle gas turbines are just below 60 percent efficiency," Soothill notes, operating at temperatures up to 1,300 degrees C.
Ceramics and air flow around the turbine itself help protect its metal components from temperatures that would otherwise melt them. "If you lose air flow, it's going to melt within seconds," Gebhardt notes.
Dry cooling all wet?
Cooling remains the major challenge for all turbines—and all power generation. Most power plants today rely on cooling water from nearby rivers or lakes—an option that may disappear as freshwater becomes more scarce or protected. For example, New York State recently required the Indian Point nuclear power plant to switch to air cooling if it wants to extend its operating life.
Unfortunately, air cooling means a big loss in efficiency. Water cooling allows for a bigger difference between the temperature of operation and the temperature of cooling, Soothill notes, which is crucial to the amount of power that can be captured. "The turbines become smaller with an air-cooled system," he says, "and you lose a bit of efficiency."
"To this day, no one has figured out a better-working fluid than water," says mechanical engineer Jaydeep Roy of GE's Structural Mechanics and Dynamics Lab. Simply put, it remains the most affordable way to spin a turbine and harvest heat. As the nation's thirst for electricity continues to grow, water may prove the sticking point—slowing the turbine's spin. |